Electric linear actuators have a variety of uses. They are an essential component in any applications that need safe, clean movement with accurate and smooth motion control.
They are easy to install and, unlike hydraulic or pneumatic systems, electric linear actuators do not use liquids, tanks, hoses or pumps; nor do they suffer oil leaks. Electric linear actuators can be used over long periods of time with little or no maintenance. They are durable and have long lifespans.
Electric linear actuators provide accurate variable control over position, acceleration, and velocity.
Electric linear actuators – how they work and their uses
Electric linear actuators have a variety of uses where a smooth, automated push or pull movement is required. There are many types of electric linear actuators, but they all essentially use the same three basic components to convertweb the rotational motion of a motor into a linear or push/pull motion.
Electric linear actuators use three main parts: a screw, gears, and motor, which can be AC or DC depending on the kind of power needed and its application. Electric linear actuators use a simple control, like a button, to send a signal to the motor, powering the gears connected to the screw. When the screw rotates, it drives the screw nut and piston rod forward or backwards, depending on the desired direction of motion.
The screw’s thread count and pitch determine the speed and load capacity the actuator can deliver. Electric linear actuators that use screws with a high thread count and small pitch will deliver slower movement and can handle higher load capacities. Screws with low thread counts and a higher pitch deliver faster movement of lighter loads.
Electric linear actuators are used in any applications requiring safe, clean movement with accurate and metered motion control. This could be anything from farming and mining equipment to baggage handling and hospital beds. They are easy to install and, unlike hydraulic or pneumatic systems, electric linear actuators do not use liquids, tanks, hoses, or pumps; nor do they suffer oil leaks.
Electric linear actuators provide accurate variable control over position, acceleration, and velocity whether pulling, pushing, lifting, or tilting. They are durable, versatile, and require little or no maintenance, even over long periods of time.
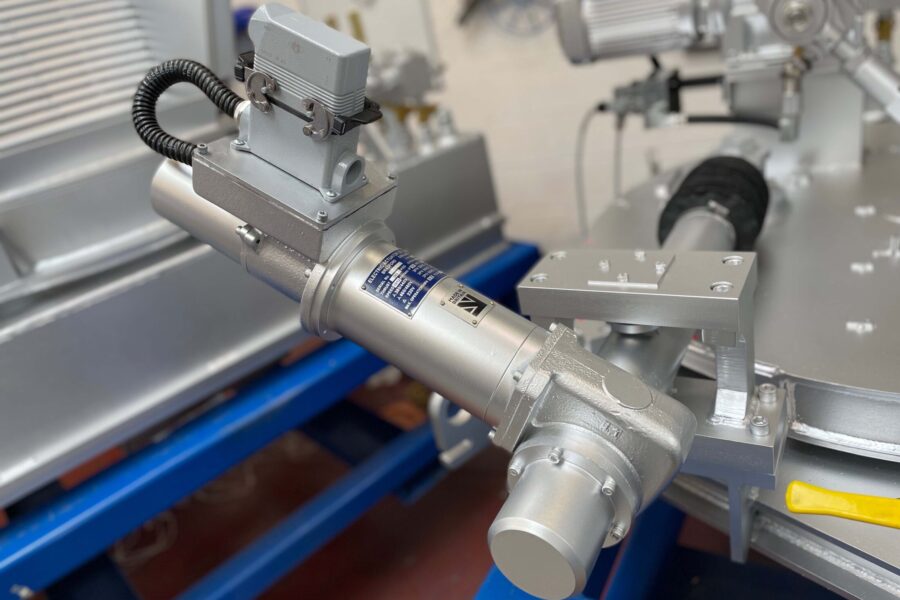
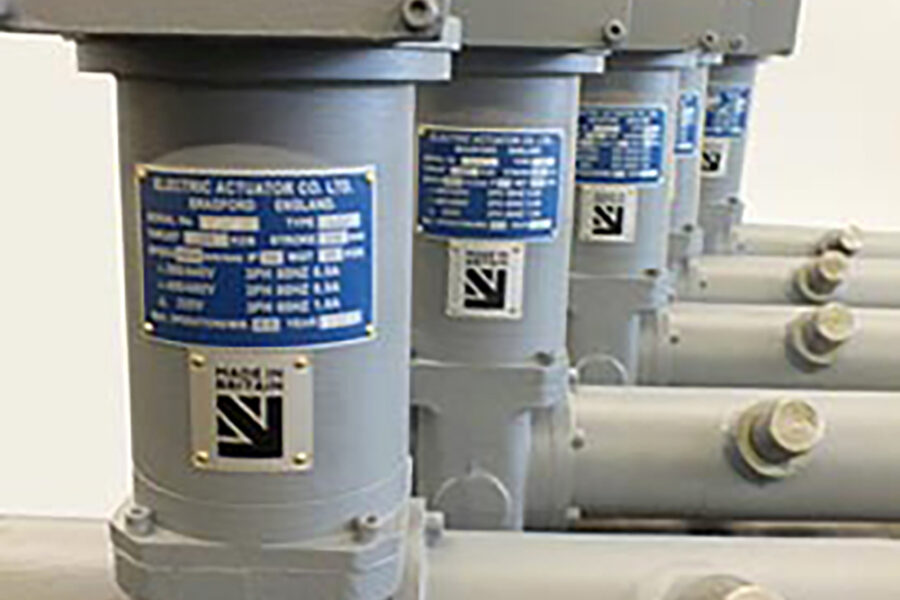
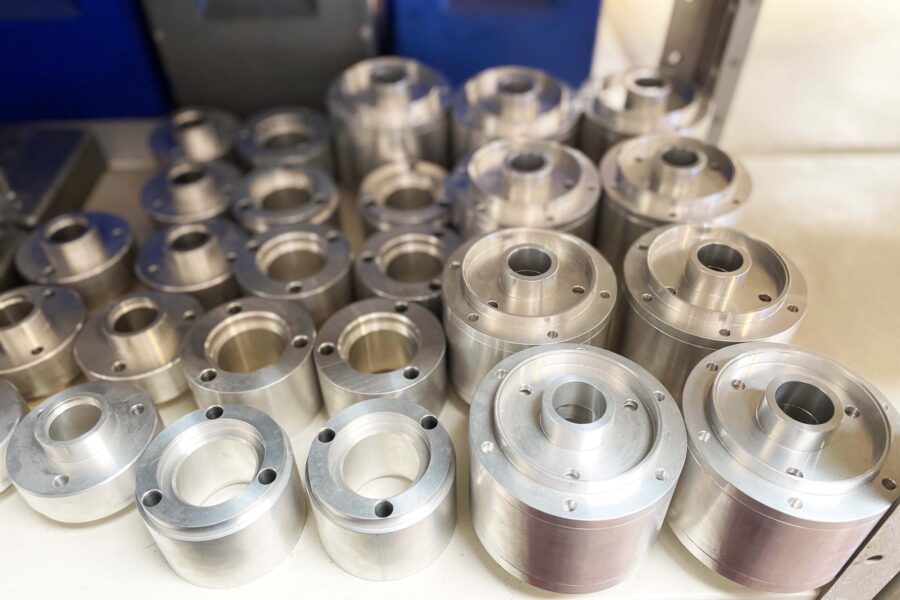
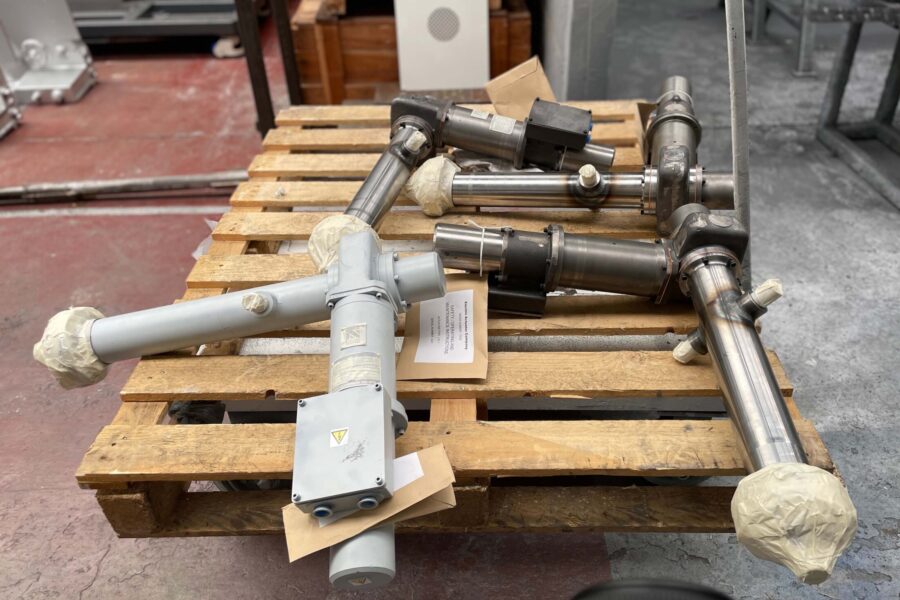
- What Industrial Sectors use Linear Actuators?
- What are the industrial uses of Electric Linear Actuators?
- What are linear actuators used for?
- Why should I use electric actuators over other kind of actuators?
- What are the different kinds of electric linear actuators available?
- What applications are linear actuators best used for?
- What applications are linear actuators unsuitable for?
- What factors can affect linear actuators when in use?
- What causes electric linear actuators to fail?
- Baggage Handling
- Biomass Production and Handling
- Cement Manufacture
- Coal/Mining Preparation
- Conveyors and Handling Systems
- Glass industry
- Iron, Steel & Glass Manufacture
- Maltings
- Mineral Processing
- Ministry of Defence
- Nuclear
- Oil & Gas
- Power Stations
- Quarrying and Aggregates
- Railways
- Sugar Processing
- Theatrical and Promotional Stage Back Drops and Equipment
- Ventilation Control
- Water Treatment
Within the sectors mentioned above, our industrial linear actuators are used for several common functions:
Solids, Liquids and Powder Flow Control:
- Control of flaps and chutes
- Control of valves and gates
- Conveyor systems
- Glass dosing equipment
- Movement of screens and large debris screens
- Movement of screens and large debris screens
- Positioners and diverters
- Sluice gate control
- Volume control
Air Flow and Ventilation Control
- Boiler and furnace dampers
- Control of valves and vents
- Isolation and retention
- Louvers and dampers
- Smoke and fire dampers
- Ventilation chutes
- Volume control
- Weather/moisture and salt spray control
Mechanical Handling:
- Carriage locks
- Control opening and closing of access doors
- Crane and grapple operation
- Door interlocks
- Operation of remote windows and doors
Position control:
- Control of trap doors, stage scenery and backdrops
- Railway de-railers
- Railway switch points
- Signalling control
Practical examples include:
- Control of hoppers and bulk storage
- Load management such as earth shoring or retention
- Management of height and tilt, such as hospital beds and variable height workstations
- The control of doors, valves, hatches and chutes
You can use linear actuators for any application requiring precise, smooth motion control with safe, clean components. Our actuators can perform a range of linear motions, including pushing, pulling, raising, lowering, sliding, and tilting.
Examples of electric linear actuator uses include earth shoring or retention; control of hoppers and bulk storage; management of doors, valves, hatches, and chutes; hospital beds and variable height workstations.
Electric linear actuators don’t use liquids, tanks, hoses, pumps, or other components. Furthermore, unlike hydraulic or pneumatic systems, they don’t suffer from oil leaks.
They are also simple to install and require little to no maintenance over their lengthy lifespans, allowing for more precise management of position, acceleration, and velocity than other systems.
Electric linear actuators keep their full force even when powered off, and do not use any electricity when idle.
There are many different linear speeds and thrust forces available for linear actuators depending on their desired uses. These are typically achieved using a combination of motor speed and torque, gearbox ratio, and screw thread pitch. Screws with low thread counts and higher pitches move lighter loads more quickly, while screws with high thread counts and small pitches result in slower movement capable of higher load capacities.
Additionally, linear actuators are customisable for a variety of uses when it comes to:
- Thrust: The maximum force the actuator is capable of in the direction of movement
- Speed: The fastest speed at which the actuator can move in and out
- Stroke: The distance the actuator moves between being fully extended and the fully retracted. This is the longest range of movement the actuator can provide.
- Precision: The degree of accuracy the actuator can attain
- Size: The overall size of the unit
Electric linear actuators can produce tension, compression, or a combination of the two forces and can be used to push or pull along the shaft’s axis. Linear actuators have various applications, from domestic to industrial; everything from adjustable car seats to coal mining equipment use electric linear actuators to achieve a smooth, linear motion.
Numerous industrial applications call for the use of our linear actuators. If you require peak performance and durability under harsh conditions, strong pressures and loads, you can count on our cutting-edge linear actuators.
Any force that is not driven parallel to the screw shaft’s axis (or centreline) will subject the actuator screw to a degree of force that’s perpendicular to the shaft. It is best to prevent side or radial loading, also known as eccentric loading, with linear actuators as this kind of use can result in binding, excessive wear, and a shorter lifespan of the actuator.
Backlash happens when a linear actuator is used in reverse, resulting in a positional error.
It’s usually caused by mechanical play in the drive train or friction in the guiding system.
Mechanical play is affected by tolerances for components such as gearheads or bearings. Several factors contribute to the degree of backlash on a linear actuator including load, direction, temperature, acceleration, and wear.
Backlash affects a linear actuator’s absolute accuracy in use. This is the maximum difference between the physical position and the ideal position. Hysteresis, drift, nonlinearity of the drive or the measurement system, and mechanical distortion can also affect absolute accuracy.
The accuracy with which an actuator resumes a position following any change in position is known as bidirectional repeatability.
Usually, electric linear actuators fail because they are being used in the wrong way. Factors including side loading, incorrect wiring, insufficient mounting, overloading, and exceeding duty cycle can all cause a linear actuator to fail in use.
FAQ’s
Find out everything there is to know about Electric Actuators and common, frequently asked questions about our products.
- What is a Linear Actuator?
- What are the applications for an Electric Linear Actuator?
- What is the difference between an Electric Actuator and a Pneumatic or Hydraulic Actuator?
- What is the difference between Static Load and Dynamic Load?
- What are the normal directions (vectors) for loads applied to Linear Actuators?
- Are side loading and eccentric loading allowed for Linear Actuators?
- Are Linear Actuators available in different speeds and thrust Forces?
- What duty cycle rating can be expected of a Linear Actuator?
- What type of mountings are available for Linear Actuators?
- Is it acceptable to run a Linear Actuator into a hard stop?
- What is absolute accuracy?
- What is backlash?
- What is bidirectional repeatability?
- What is the power consumption?
- What is the push/pull force?
- What is the push/pull speed?
- What is stroke?
- What is motor speed?
- What is motor power?
An electric linear actuator converts the rotational motion of a motor into the linear motion of a rod that moves forwards and backwards, providing push and pull forces in those two directions. The actuator can be stopped at any time during its movement, although the maximum holding force must be considered.
A linear actuator can lift, tilt, push, or pull objects using electric control. Industrial linear actuators are often used in hazardous environments or to manage heavy or extreme loads. Actuators are accurate, efficient and have a long lifetime.
An actuator’s key components are as follows: motor, reduction gear, lead screw, drive nut and push/pull tube. As the motor and gearbox rotate the lead screw, the drive nut extends and retracts the push/pull tube, which is then attached to the load.
Electric linear actuators are used in any applications that need safe and clean movement with accurate and smooth motion control. They are easy to install and, unlike hydraulic or pneumatic systems, do not require liquids, tanks, hoses or pumps, nor do they suffer oil leaks. They have long lifetimes with little or no maintenance.
They provide accurate variable control over position, acceleration and velocity.
Practical examples include the control of doors, valves, hatches and chutes; load management such as earth shoring or retention; control of hoppers and bulk storage; management of height and tilt, such as hospital beds and variable height workstations.
Both pneumatic and hydraulic actuators use fluid or compressed air to push a ram backwards and forwards. An electric actuator uses a motor to drive a lead screw which converts rotary motion into linear motion. Electric Actuators can maintain full thrust with power off and will not consume power when not operating.
Static load (also called the holding load) is the force applied to the linear actuator when it is not in motion. Dynamic load (also known as working or lifting load) is the force applied to the linear actuator while it is in motion; or to put it another way, it is the force that can be applied to push or pull something.
Electric linear actuators can be used to push or pull along the axis of the shaft and can provide tension or compression forces, or a combination of both. Eccentric and side loading should be avoided.
Any force that is not applied along the axis (or centreline) of the screw shaft will have an element of that force which is perpendicular to the shaft. That side or radial loading, also called eccentric loading, should be avoided as it can cause binding, excessive wear and shorten the life of the linear actuator.
Linear actuators are available in a variety of linear speeds and thrust forces; these are usually designed in through a combination of motor speed and torque, gearbox ratio and screw thread pitch.
The duty cycle rating for a linear actuator is normally expressed as cycles per minute or a percentage of the ‘on time’ (the ratio of on time to total time).
A linear actuator can be mounted using a Trunnion mount, end swing pin, front flange mount or side flange mount.
Special mountings can be designed to suit applications. Electric actuators can also be mounted in any orientation.
Generally, no. This can damage the internal screw or drive nut, damage the gearbox, or overload the motor.
Our linear actuators operate in a wide range of different industrial applications. We are typically the linear actuator solution of choice where durability, high forces and loads, and the ability to perform in extreme environments are critical factors.
Absolute accuracy is the maximum difference between the actual position and the desired position. It is affected by issues such as: backlash, hysteresis, drift, nonlinearity of the drive or the measurement system, and mechanical distortion.
Backlash is a positional error that is evident when reversing direction. Its causes are mechanical play in the drive train or friction in the guiding system. Mechanical play is influenced by tolerances for components such as gearheads or bearings.
Several factors affect the amount of backlash: load, direction, temperature, acceleration and wear.
Bidirectional repeatability is the accuracy with which an actuator returns to a position after any change in position.
Power consumption refers to the maximum power consumption under a full load.
Push/pull force refers to the maximum force delivered by the actuator in the direction of motion.
Push/pull speed refers to the maximum speed at which the actuator can extend and retract.
Stroke is the distance between the fully extended actuator and the fully retracted actuator – the maximum length of movement that the actuator can supply.
Motor speed is the maximum rotational speed of the motor, expressed as rpm (revolutions per minute).
Motor power is the maximum power consumed by the motor when the actuator is operating under a full load.